Steel Surfaces Coatings Systems
Good surface preparation is the most
decisive factor for coating successfulness. Another decisive factor is the
selection of a suitable finishing coat adapted to the end use requirements.
Metals exposed to severe weather conditions will be treated differently from
these exposed to mechanical stresses or to chemicals.
Metals are classified under two broad
headings, ferrous (iron and steel) and non-ferrous metals (galvanized steel,
aluminum, etc...).
STEEL:
Iron and steel may rust if they come in
contact with moisture and oxygen. The presence of certain contaminants such
as chloride and sulfate ions as well as the gaseous oxides of sulfur and
nitrogen, which are present in marine and industrial atmospheres,
accelerates the corrosion rate of steel.
The durability of paint applied to steel
is affected by the surface condition of steel immediately prior to painting.
Three principal factors are to be considered when coating steel structures:
- The presence of rust and / or mill scale;
- The presence of surface contaminants including salts, dust, oils,
greases, and loose paints;
- The surface profile (too smooth “ glossy surface”).
Different standards have been prepared
to provide methods of assessing these factors, the Old Swedish standard SIS
05 59 00 – 1967, the German standard DIN 55928), the British standard
BS7079, and the International standard ISO 5801-1: 1988.
The Old Swedish standard SIS 05 59 00 –
1967 and the ISO 5801 are used on worldwide scale for visual assessment of
rust grades “rust and mill scale levels that are commonly found on surfaces
of uncoated steel”. They are used also for visual assessment of preparation
grades “the visual cleanliness after surface preparation of uncoated steel
and of steel surfaces after overall removal of any previous coating”. ISO
5801 includes 28 representative photographic examples, 24 of the photographs
originate from the Old Swedish standard SIS 05 59 00 – 1967 and the other 4
photographs originate from the German standard DIN 55928.
Rust Grades:
The ISO 8501-1 identifies four levels of
rust grades and mill scale that are commonly found on uncoated steel
surfaces and on steel surfaces after overall removal of any previous
coating. The levels of visual cleanliness are related to the methods of
surface cleaning that are used prior to coating.
A Steel surface largely covered with
adhering mill scale but little, if any, rust.
B Steel surface which has begun to rust
and from which the mill scale has begun to flake.
C Steel surface on which the mill scale
has rusted away or from which it can be scraped, but with slight
pitting visible under normal vision.
D Steel surface on which the mill scale
has rusted away and on which general pitting is visible under normal
vision.
Preparation grades
1-Mechanical methods
Different preparation grades are provided by the international
standard ISO8501-1 indicating the method of surface preparation and
the degree of cleaning. Two mechanical methods are mostly used:
A-Blast-cleaning, Sa (sand blasting)
Prior to blast-cleaning, steel surfaces
must be cleaned from oil, grease, and dirt. Heavy layers of rust should be
removed by chipping.
Sa 1 Light blast-cleaning:
The surface should be free from visible oil, grease and dirt,
and from poorly adhering mill scale, rust, paint coatings and
foreign matter.
Sa 2 Thorough blast-cleaning
The surface should be free from visible oil, grease and dirt,
and from most of the mill scale, rust, paint coatings and
foreign matter. Any residual contamination shall be firmly
adhering.
Sa 2½ Very thorough blast-cleaning (to near white metal)
As Sa2 but any remaining traces of contamination shall show
only as slight stains in the form spots or stripes.
Sa 3 Blast-cleaning to visually clean steel (to white metal)
The surface should be free from visible oil, grease and dirt,
and from most of the mill scale, rust, paint coatings and
foreign matter. It shall have a uniform metallic color.
B-Hand and power tool cleaning, St
(Scrapping, wire-brushing, machine-brushing and grinding)
Prior to hand and power tool cleaning,
steel surfaces must be cleaned from oil, grease, and dirt. Heavy layers of
rust should be removed by chipping.
St 2 Thorough hand and power tool cleaning
The surface should be free from visible oil, grease and dirt,
and from most of the mill scale, rust, paint coatings and
foreign matter.
St 3 Very thorough hand and power tool cleaning
As for St2, but the surface should be treated thoroughly to
give a metallic sheen arising from the metallic substrate.
Notes:
1- In general and depending on the recommended end use, cleaning of
large or flat areas to Sa2½ or Sa2 or even St2 could be
sufficient. While cleaning of corners and small areas require higher
degree of cleaning such as to Sa3 or St3.
2- Steel surfaces coated by the same material will last three times
if blast cleaning (to Sa3) is used instead of wire brushing (to St3).
3- After blasting or hand and power tool cleaning, the surface shall
be cleaned from loose dust and debris.
2-Chemical methods:
Table 1: Ferrous and Steel
substrate treatment
Use |
Product |
Remarks |
Rust Cleaning Agent |
SIP Rust Cleaner |
Rapidly removes rust from ferrous metal and Stainless
steel. |
Rust Converting Agent |
Rust Convert |
Converts chemically tightly adherent rust into a non
rusting black film. |
Metal cleaning agent |
Gel Cleaner |
Removes rapidly rust, stains, mineral deposits, oil and
grease from metal substrates highly recommended for
vertical surfaces. |
Cleaned and blasted steel
surfacesrequire priming and coating in order to protect the
steel surface from corrosion. Painting operations or at least
the application of a protective primer have to be performed
within few hours of blasting to ensure that surface rusting does
not recommence.
Primer thickness depends on the profile
of the roughened steel. With coarser profiles, it is important to ensure an
adequate paint coating thickness in order to ensure that peaks of the
roughened surface are coated.
As steel surfaces are recommended to be
coated for different applications such as home and office equipment,
structural members for buildings, pipes, tank exteriors, storage tanks and
reservoirs, marine equipment, oil refineries, …etc. The selection of a
suitable paint system for each of this diversity of end uses, each with
their own specific performance requirements, is a must.
ALUMINIUM And GALVANISED STEEL:
Aluminum and galvanized steel are
difficult to paint metals. They must be degreased with a special cleaner
such as Gel Cleaner then rinse well with water. Prime dry substrate with a
tie coat such as wash primer (WP) in order to improve the adhesion between
the metal and the paint system.
ANTI-CORROSIVE PRIMERS
Different kinds of anti-corrosive
primers are provided by Azmeh Co. and listed in Table2. They differ in their
anti-corrosive strength, adhesion and chemical nature (Figure 1).
Table 2
Product
|
Description
|
Recommended Use With
Suitable Topcoat
|
SYN203 Red Metal Primer
|
Alkyd primer containing iron oxide.
|
Interior and exterior use in domestic and mild
industrial atmospheres on steel and iron surfaces.
|
SYN210 Red Lead Primer
|
Alkyd primer containing lead oxide.
|
Exterior use only in mild industrial atmospheres
on steel and iron surfaces.
|
WP “Wash Primer”
|
Two component primer based on
polyvinyl resin and phosphoric acid hardener.
|
Excellent adhesion properties, suitable for
almost all kinds of metal surfaces such as steel, galvanized
steel and Aluminum. Used on all conditions: interior, exterior,
and for immersion and non- immersion service.
|
SIP900
|
One component epoxy primer containing zinc
phosphate.
|
Easy to apply, recommended for mild to severe
weather conditions and for non-immersion service in marine and
industrial atmospheres.
|
EPX02 White
|
Two component epoxy primer containing zinc
phosphate.
|
Highly adherent on metal surfaces with good
abrasion resistance, recommended for immersion and
non-immersion services in marine and industrial atmospheres.
|
EPX12 Alu |
Two component Aluminum
epoxy primer / coat |
Recommended for immersion and non-immersion
services in marine and industrial atmospheres. Suitable to be
applied on steel surfaces where blast cleaning is not feasible. |
EPX01
|
Two component zinc rich epoxy primer
|
Excellent corrosion resistance, used in marine
and industrial atmospheres. Not recommended for immersion
service and where abrasion resistance is required.
|
INOZINC |
Two component water
base Zinc silicate primer |
Highly recommended in area where fast cure and
excellent corrosion resistance primer is required, provides long
term protection in marine environments. Suitable for use in
areas exposed to high humidity. |
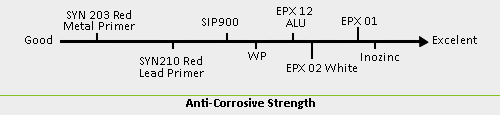
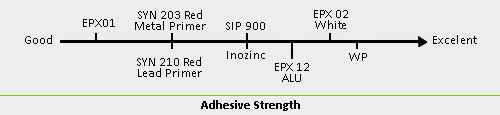
Figure 1
|Top|
FINISHING COAT
Finishes for steel are based on
materials selected to withstand the conditions likely to be experienced in
the proposed service environment. Steel surfaces exposed to severe weather
conditions or to mechanical wears or to chemicals require different coating
systems.
Pipe and tank lining systems are listed
in Table3:
Table 3
END USE
|
Primer
|
Lining Coat
|
1- Aggressive water service "salt and
brackish" in tanks and all marine structures and also where chemical
resistance is required (refer to
CHR01 table for chemical resistance). |
WP*
or EPX02 White
|
EPX105GF (With CAT22)
or EPX105GF (With CAT32)
|
2-Pipe and tank lining containing salt water or
irrigation water.
|
WP*
|
EPX14
|
3-Pipe and tank lining containing Oils & chemicals
|
WP*
|
EPX33 (With CAT20)
|
Or WP* |
EPX36 (With CAT20) |
Or WP*
|
EPX24 |
Or WP*
|
EPX04 |
4-Tank lining containing food & beverage.
|
WP*
|
EPX33 (With CAT30)
|
Or WP*
|
EPX36 (With CAT30)
|
Table 4 shows the recommended coating
systems for interior and exterior exposure. Exterior exposure can vary from
mild to severe and extremely severe or hard weathering.
Table 4
END USE
|
Primer
|
Topcoat
|
1-Internal dry exposure
Decorative for home and office equipment.
|
-
Not recommended
|
ALDAHAB 205 Coat Or SHR Or
ALDAHAB 205 Coat + Drier205
Azure coat Or SYN Hammer Finish
|
2-Industrial and domestic appliances, where a high
degree of abrasion resistance and resistance to heat, water, and
cleaning materials are required.
|
EPX02 Gray (optional)
Or Not recommended
|
EPX03
|
Or ALDAHAB 205 Coat (with "drier 205") |
STOVING ENAMEL
|
3-Industrial appliances where corrosion
resistance is required
|
SYN203 Red Metal Primer
Or SYN210 Red Lead Primer
|
ALDAHAB 205 Coat Or SHR Or Original Z117-Z127-Z137
|
4-Steel Structures, where excellent resistance to
corrosion, light chemicals and mechanical wears are required.
|
WP Or EPX02 White
Or
Not recommended
|
EPX03 Or EPX13
|
5-Steel structures, where excellent corrosion and
chemical resistance are required and exposed to severe weather
conditions.
|
EPX01 + EPX02 Gray
Or Inozinc
Or EPX02 White
|
HARDTOP
|
6-Steel structures exposed to mild to severe
weather conditions and mechanical wears.
|
SIP900 (if required)
Or WP if immersion
|
C. Rubber "RUB"
|
7-Buried steel, pipes, and tanks.
|
WP*
|
EPX14
|
8-Immersed steel, pipes, and tanks in:
a-Water, salt and sea water
b- Oils and chemicals
|
WP*
WP*
|
EPX14
EPX24 or EPX04
|
9-Steel materials such as furnaces, heat
exchangers, hot pipes exteriors and exhausts, …etc, where high heat
(up to 600?C) and excellent weathering resistance are required.
|
Not recommended
|
THR
|
10- Protection of steel surfaces from fire in addition to its
excellent resistance to weathering and corrosion.
|
WP
|
FireProtect
Or Fire Protect Ultra (Intumescent
Paint)
|
Note:
*WP Wash primer is used if coating is not possible immediately over recently
blasted steel
|